If you’re interested in the science behind manufacturing glass, this article is for you. The type of glass used for decorative pieces tends to be far more brittle than its reinforced alternatives, toughened glass, and safety glass. But what changes need to be made when manufacturing glass to achieve these different types?
In this article, we discuss how the different types of glass are made and the properties of each type.
How is it made?
Glass is made from a combination of natural raw materials, including sand, soda ash, and limestone. These materials are melted at 1700°C to create liquid glass, which is then blown, pressed, moulded, and cooled. But depending on the type of glass you want, the process will alter.
Ordinary glass
Manufacturing ordinary glass, otherwise known as soda glass, is done as we previously described. Ordinary glass is most often made of recycled glass and sand, but the requirements for specific applications often call for the use of different materials.
If you’re manufacturing glass to be green or blue in colour, iron oxide, and cobalt are added to the mixture. The most commonly used type of glass is soda-lime glass, which combines soda ash, silica, limestone, dolomite, and glass cullets.
Glass made this way is unsuitable for use as a protective measure, and cannot be stood on. However, other types of glass can adhere to these requirements.
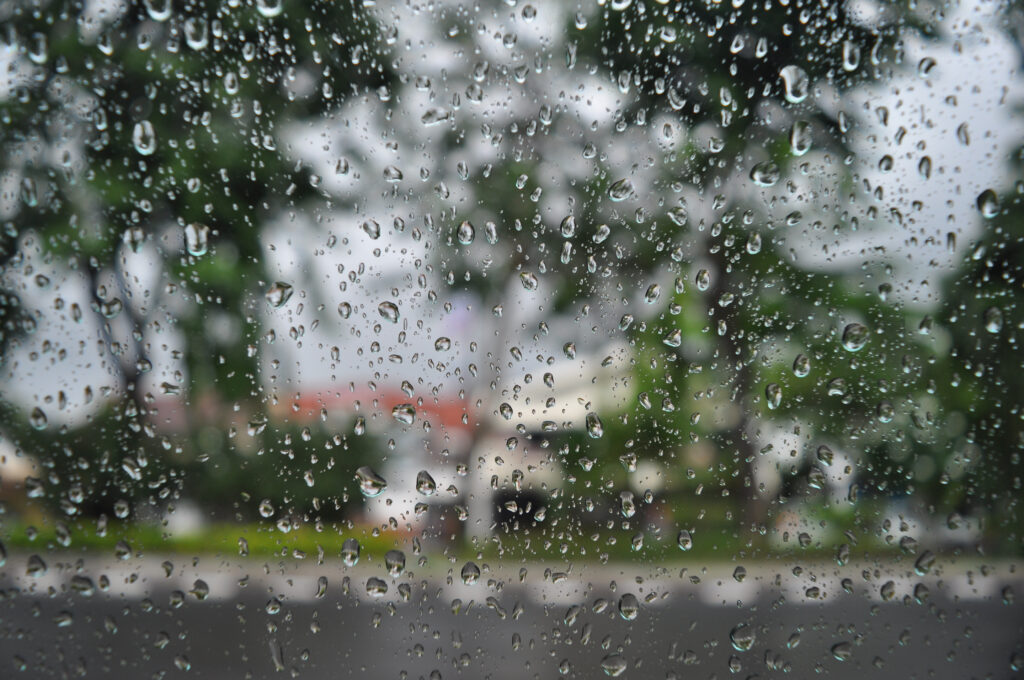
Borosilicate glass
Borosilicate glass is the type of glass you find in oven-proof glass dishes. Ordinary glass would not be able to withstand the constant heat of an oven without shattering or exploding due to thermal shock.
Borosilicate glass can handle high temperatures due to the boron oxide content. Boron oxide boasts a melting point of 450 °C. So it is more than capable of resisting extreme heat.
Coloured glass
Manufacturing glass in an array of colours depends on a series of metallic compounds. When particular molten metals are added to glass, they change the colour of the glass. This is because the ions in the metals absorb different wavelengths of light.
Iron Oxide imparts a blue-ish green colour.
Sulfur mixed with carbon and iron salts makes yellow or black (depending on the ratio).
Magnese creates an amethyst colour when added in high concentrations.
Chromium makes green.
Cobalt makes blue.
Silver Nitrate creates orange.
The chemistry behind coloured glass is exceedingly interesting! But most cheap coloured glass is simply stained.
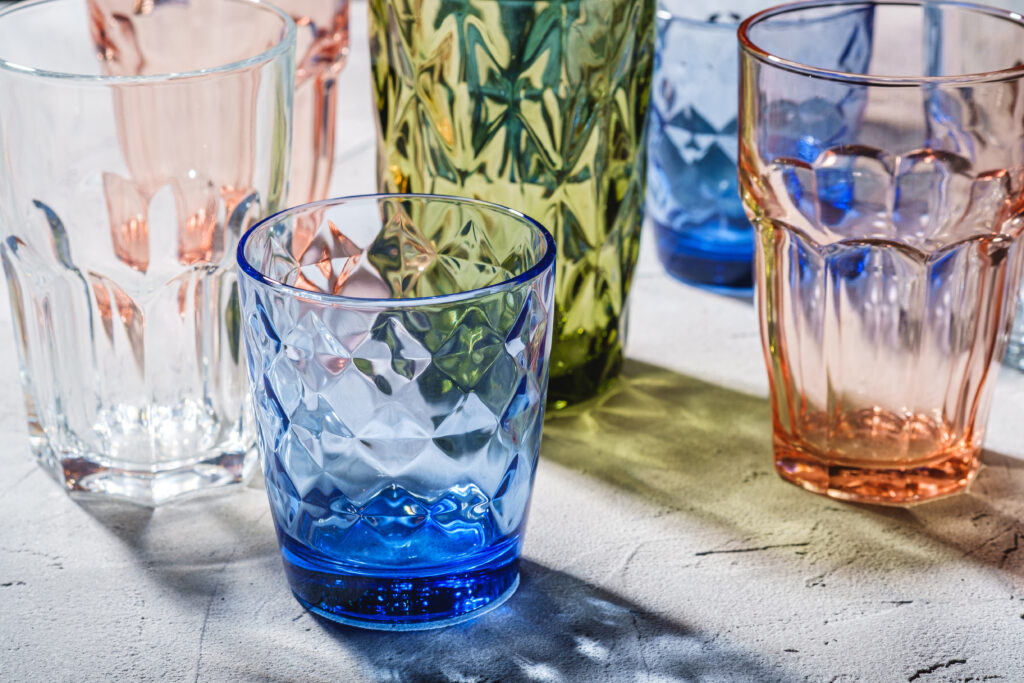
Annealed glass
Annealed glass is a type of glass that has been thermally treated and slowly cooled to avoid thermal shock. This is the type of glass you see being used for tabletops and cabinet doors.
Should annealed glass break, it will do so into shards, which can cause significant injury. It is often used as a cost-effective solution in areas where safety is not a priority.
There is often some confusion between annealed glass and tempered glass, as manufacturing glass of these types tends to be a very similar process. But it’s actually quite different.
Toughened glass
Toughened glass, otherwise known as tempered glass, is heated to 600°C and endures a cooling procedure called “quenching” to encourage the process of compression, which makes toughened glass four times stronger than annealed glass.
Annealed glass breaks at 6,000 per square inch (psi), but toughened glass can withstand more than 10,000 psi, and only tends to break at 24,000 psi. Furthermore, when tempered glass does break, it does so into small blunt shards and doesn’t pose the risk of injury like annealed glass.
Compression can also be achieved by mixing various chemicals on the surface of the glass and allowing their ions to exchange, which will cause compression.
Toughened glass is commonly used for balcony doors, athletic facilities, bathroom fixtures, exhibition displays, and roof lanterns.
Safety glass
Safety glass, also known as laminated glass, is made by conjoining two or more layers of glass together using a chemical bond that can only be achieved with a PVB resin interlayer.
The PVB resin interlayer maintains optical clarity and enhances toughness and flexibility within the glass. PVB is somewhat impenetrable, as it is incredibly difficult to cause it to break. If the glass does break due to sudden and extreme impact, the glass will not shatter at all. The shards will remain contained in the glass.
Safety glass is incredibly UV resistant and minimises noise exponentially. This makes laminated glass a fantastic choice for low-level windows, car windows indoor glazing, glass stairs, and walk-on rooflights.
Manufacturing glass that is intended for use as a bulletproof protective measure requires the same process as safety glass. The only difference is a layer of polycarbonate between the panes to absorb the shock of a bullet.
The process of manufacturing glass of all types is incredibly complex and interesting. It is very compelling to see how simple changes can completely affect the suitability of use for different purposes. Here at The Rooflight Centre, we use several of these glass types for our rooflights to ensure they’re as durable as can be. Contact us now if you’d like to learn more!
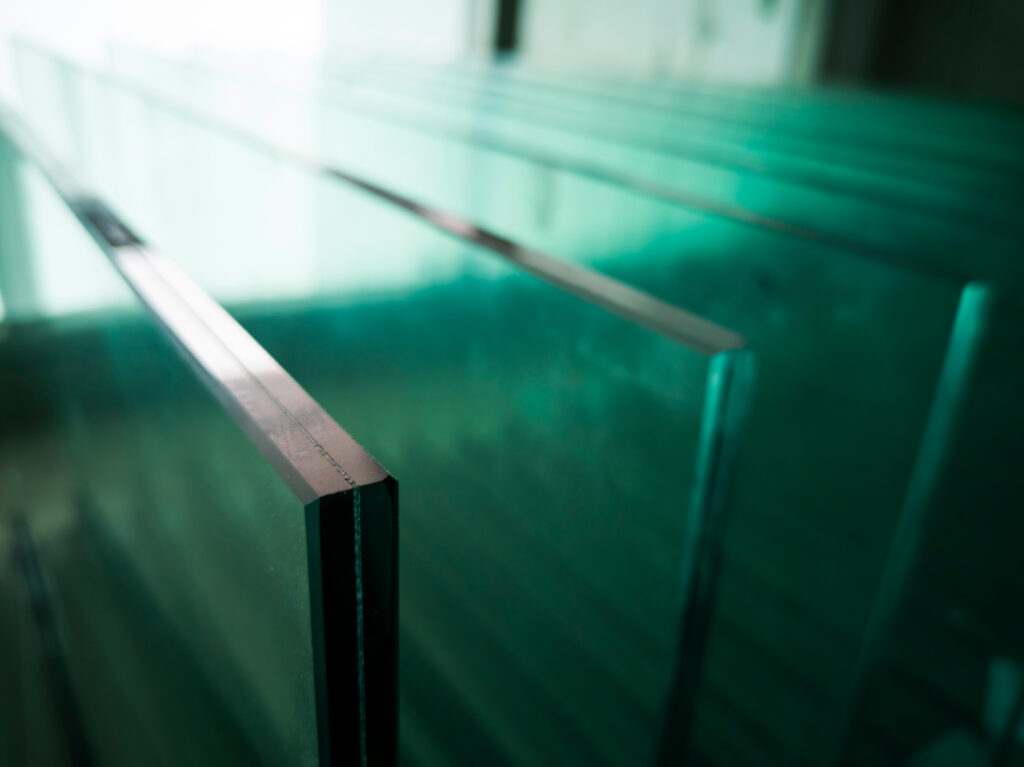
Wired glass
The process of manufacturing glass including wiring is possibly the most simple method on our list. Wired glass is simply annealed glass with an embedded wire mesh that provides additional reinforcement to prevent the glass from shattering.
The wire makes the glass stronger and more durable, and is often used in the partitions of windows in schools, hotels, and institutions. The wire also acts as a fire retardant and keeps the glass held together in situations where thermal stress may occur and cause the glass to explode.
Self-cleaning glass
Manufacturing glass that is self-cleaning relies on pore size and hydrophobic chemical coatings. The pores of self-cleaning glass are much smaller so as not to collect dirt, and the chemical coating titanium dioxide reacts with the UV light from the sun to break down any organic dirt which may be collected.